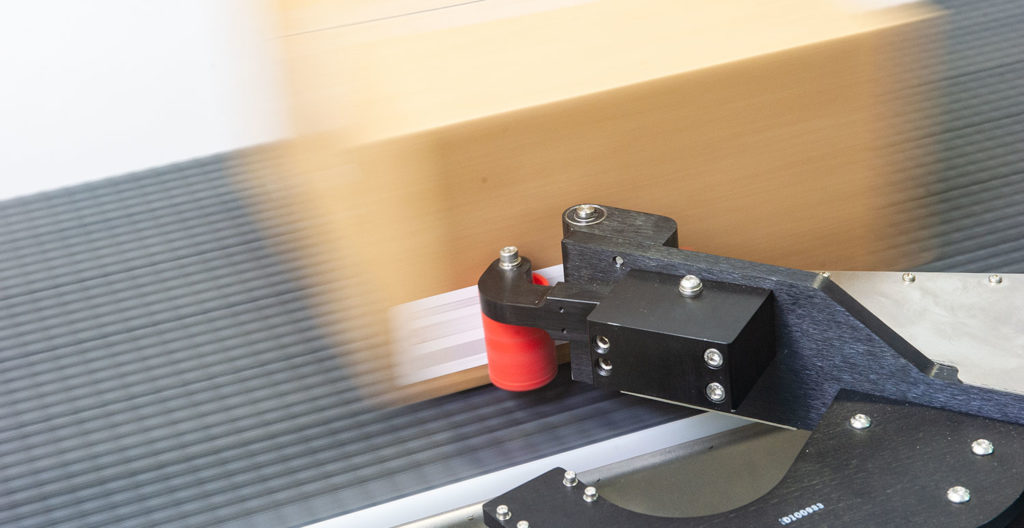
When it comes to adding barcodes to your corrugated shipping cases, the two most common ways to do this are to either use labels or print directly to the box using an inkjet printer, depending on your product and industry.
As with many things, the answer is that it depends.
Which method is best?
Let’s take a look at reasons to choose one technology over the other.
Where do your barcodes need to be placed?
If you need to comply with GS1 standards for your customer’s barcoding requirements, you will have to ensure that each corrugated shipping case has two compliant barcodes. These can be placed on either opposite sides of the box or adjacent sides.
It is straightforward to install a pair of either labeling or inkjet systems on each side of the conveyor to meet the requirement for opposite-side labeling.
It isn’t so easy for inkjet when it comes to adjacent faces, or maybe the leading or trailing face.
While label applicators can be configured for this, the case would need to be turned on the conveyor to get the correct face adjacent to the printhead if using an inkjet printer. This adds more complexity and possibly means more conveyor length is needed.
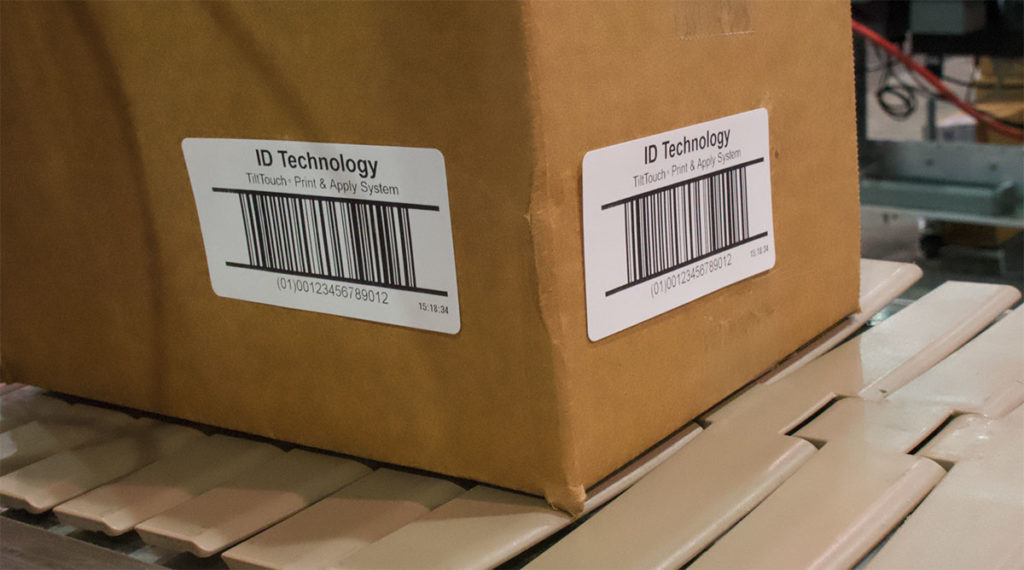
A labeling system such as ID Technology’s TiltTouch™ or Panther’s Predator Swing Applicator is often the best solution for labeling adjacent sides of the product.
These label applicators are specially designed to label adjacent sides of a shipping case, as it passes on the conveyor.
How is your product handling?
All case coding systems perform at their best with good product handling. Still, labeling is somewhat more forgiving – although some designs such as TiltTouch rely on reasonable product control.
Because of the limited throw-distance of inkjet heads, these printers demand excellent product handling to get good results.
If there are doubts about the suitability of your current product handing, discuss with your ID Technology representative – we can certainly help.
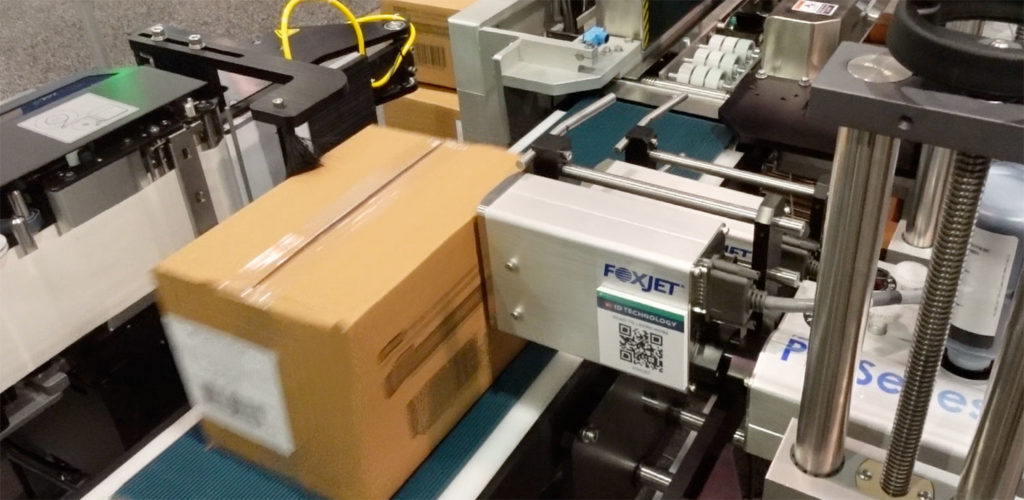
What barcode symbology do you need to print?
The chances are that you will need to print either a GTIN-14 barcode or a GS1 128 on your package. It’s important to know which you have to use. While both inkjet and labeling technologies do an excellent job with GTIN-14 barcodes, inkjet is not usually recommended for the higher density GS1-128.
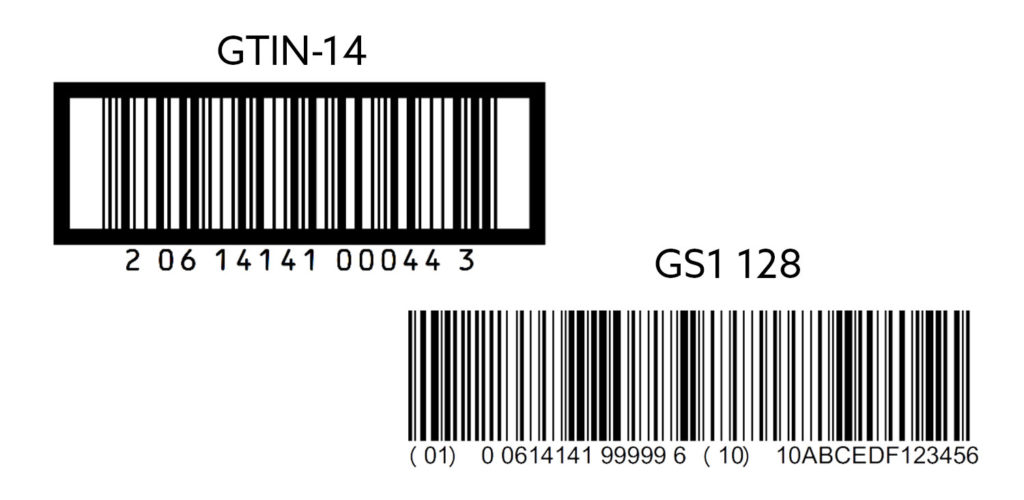
Your customer will usually tell you which barcode to use, although some industries often have specific requirements such as the protein and fresh produce industries which both use GS1 128 barcodes, where labeling is the ideal method.
What about barcode quality?
When printing barcodes that need to be scanned in distribution chains, it is vital that your codes are correctly encoded and that they meet the quality standards, both of GS1 and your customer.
While most companies require barcodes to comply with the GS1 standard, some (Walmart is a good example in some cases) insist on a higher quality standard.
Linear barcodes such as GTIN-14 and GS1 128 are graded against ISO15416, which is very similar to the old ANSI standard you might have used in the past.
When verifying the quality of a barcode using a barcode verifier, a number of attributes are tested, and a single score is returned. The overall score for a particular barcode is produced by taking the individual scores of each parameter and setting the single lowest score.
Under the ANSI system, this would be a letter score (A – F), whereas the ISO standard returns a numeric score.
When printing with black(ish) ink on a brown corrugated material, the contrast is not as high as printing in black on a white label. Since contrast is one of the attributes that make up the barcode score, direct inkjet print on corrugated boxes will generally not reach as high a quality score as a nicely printed label.
One might think that this might be a big negative inkjet printing on cases, but wait – GS1 has us covered.
For the GTIN-14 barcode (the only one suggested for inkjet printing on corrugated), our friends at GS1 have adapted the quality score to match real-life and allowed a lower passing score:
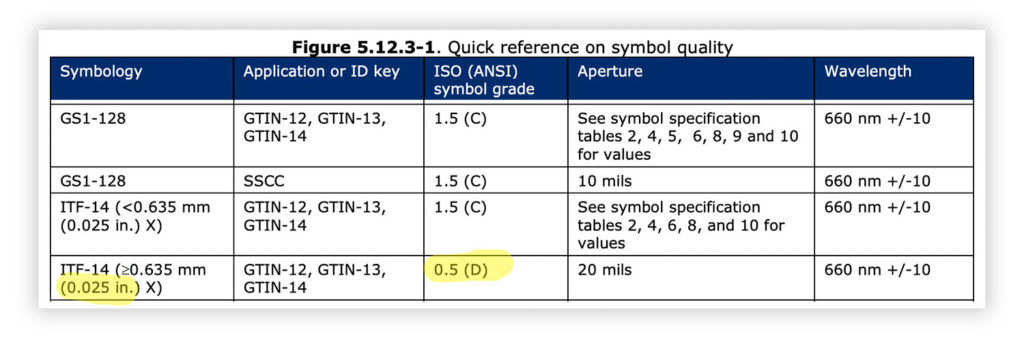
This is one of the quick reference tables in the GS1 General Specification and you can see that the passing grade for most barcodes is 1.5 (or C in the old ANSI standard), but for GTIN-14 barcodes (with an x-dimension greater than 0.025 inches), the passing grade is reduced to 0.5 (D).
This means that directly printing to corrugated using an inkjet printer such as our ProSeries is viable and can easily produce barcodes that meet the GS1 specs.
What about costs?
Well, the ink used to add a typical GTIN-14 and some text to a corrugated shipping case using a ProSeries printer will be less than the cost of a label (and possibly thermal ribbon) for a print apply labeling system.
If the cost per print was the only factor, everyone would always use inkjet. However, product handing, type of barcode, location of the barcodes on the product, and barcode quality needs (not all the big retailers will always accept the 0.5 quality scores for GIN-14) all need to be considered.
This year has seen excellent sales levels for our print/apply labelers and our case coding inkjet systems, so our customers are invested in both technologies.
Which do you use? Do you have a feel for which would work best for you?
If you need help, contact us at IDT@ProMachBuilt.com or you can message me at LinkedIn
Either way, we’ll get you connected with the best person to help and if you want to learn more about GS1 barcodes, check out the ID Technology Introduction to Barcodes eBook.