What on earth is late-stage customization in packaging? If your company packages anything that has a date or lot code, or maybe a barcode printed at the time of packaging, you are probably using late-stage customization techniques already.
A common usage of late-stage customization is using generic packaging materials, adding the printing right when the package is filled.
Before going into detail on late-stage customization, let’s quickly look at why it is becoming more critical – especially for companies implementing lean manufacturing procedures.
Modern Manufacturing.
Manufacturing is far more sophisticated than in the past. Many manufacturers have implemented lean techniques, and late-stage customization can dramatically help:
- Reduce (ideally eliminate) waste – late-stage customization produces finished packaging materials only when needed.
- Reduce overproduction – since the finished printed package is printed at the moment of use, overproduction is dramatically reduced.
- Hold less inventory – no need for multiple inventory items; late-stage customization can radically reduce the number of SKUs in your inventory.
- Eliminate unnecessary motion – less getting rolls or other materials from inventory—reduced need to remove and replace packaging materials from equipment.
- Keep defects to a minimum – fewer machine settings between production runs, fewer defective items produced during setup.
- Reduce over-processing
- Reduce waiting times – no waiting for materials to be brought from inventory for the next job; just complete a digital setup and get ready to run.
- Avoid unnecessary transport of materials – less internal movement of materials from inventory and production.
In addition, manufacturing is expected to be more flexible – be able to cope with increases in the number of SKUs and smaller batch or lot sizes, leading to more product changeovers and shorter run times on equipment.
Let’s look at some typical late-stage customization applications.
Late-Stage Customization.
For this article, late-stage customization involves using generic packaging materials that are printed with the correct information at the time of packaging – or very close to it.
Common examples include using inkjet printers to add date or lot codes to food products, printing and applying a barcode to a shipping case at the time of packaging, or adding FDA UDI barcodes to medical device packaging when the package is filled on the packaging line.
Where late-stage customization comes into its own is when the technique can remove the need to have to purchase pre-printed packaging materials.
Here are some concepts from our ProMach brands:
Eliminate the need to purchase pre-printed corrugated materials.
Some companies purchase multiple SKUs of pre-printed materials for their shipping cases.
Not only is this expensive, but it creates waste if the copy needs to change while there are still items in inventory. In addition, inventorying a unique case for every SKU takes up a lot of space. It causes production delays if there is an ordering problem, or the supplier misses a delivery deadline.
The late-stage customization solution uses a direct-to-case inkjet system, such as our ClearMark HR.
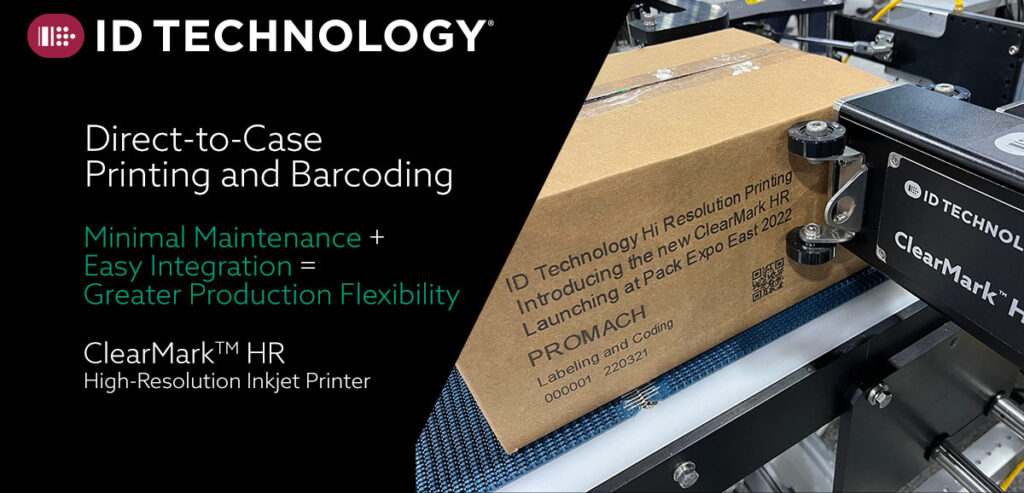
ClearMark HR is the latest generation of case coding equipment and can print an area of up to 8 inches high (using a pair of 4-inch high printheads). By introducing ClearMark HR, many customers have dramatically reduced the number of printed items they need to manage – one recent project allowed our customer to go from 140 items to about 20.
As well as reducing waste, inventory and waiting times, the all-digital workflow of ClearMark HR keeps your printing process totally under control, helping to reduce errors as well.
Even if you wish to keep your printed materials, ClearMark HR and our print/apply labeling systems are ideal for adding GS1 standard barcodes to your secondary packaging.
Late-stage customization for medical device packaging.
There are excellent opportunities to improve lean manufacturing using late-stage customization techniques in the regulated medical device industry.
It is common for medical products to be packaged using flexible materials such as films, foils, or Tyvec.
Because medical device companies need to meet strict labeling mandates for their markets, it can be challenging to manage all the variations of pre-printed packaging material that are required.
Switching, instead, to on-demand printing, right on the packaging machine is a great way to implement late-stage-customization and take advantage of all the improvements to your lean manufacturing it brings.
Our Greydon Genesis family of digital printing systems provides a 100% digital workflow and works with your artwork management software, such as Prisym ID.
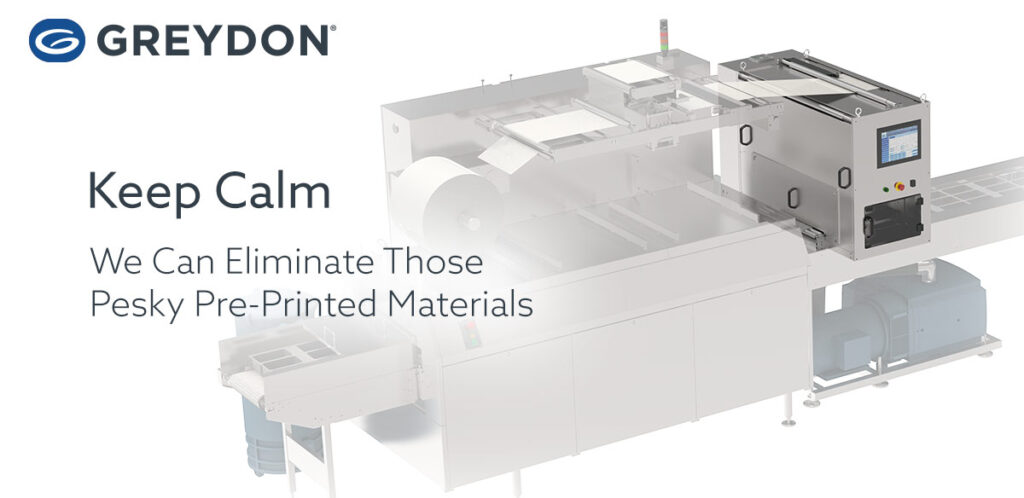
Genesis is engineered to integrate with just about every horizontal packaging or blister machine and can be confused to print single color or beautiful full process CMYK.
With the ability to print multiple packs across the web, Genesis allows the complete package to be printed and variable data for UDI and EU MDR compliance.
Saving on setup time and having to continually move pre-printed rolls of material, as well as being able to respond faster to regulatory changes, makes Genesis an ideal solution to bring the benefits of late-stage customization to your business.
Since we are looking at the Greydon Genesis, here is a link to a previous article where we teamed up with ProMach brand, Matrix, to develop an integrated sachet packaging and printing system to bring lean manufacturing concepts to stickpacks and sachets.
Late-Stage Customization for Food Labeling
It’s widespread in the food industry to package products in trays or pouches, often with a label on both sides of the package.
Usually, the label on the top of the package is flexo or digitally printed – it includes nice graphics and branding.
The bottom label is where important regulatory information is found – ingredients, nutrition information, and the critical allergy warnings.
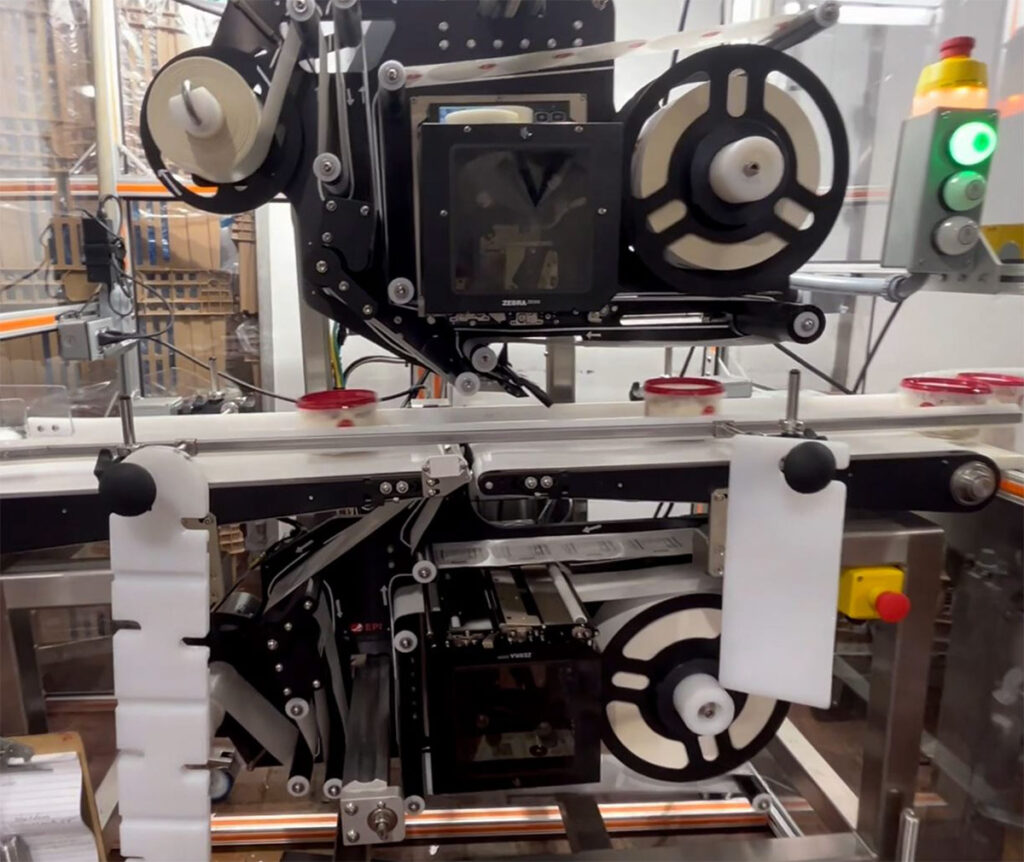
How can you take advantage of late-stage customization for this labeling job? Easy, actually – by using one of our EPI MFlex labelers, with a thermal print engine added to the labeling head, you can print all the variable information (nutrition, ingredients, allergens, date codes, etc., to a blank or generic label – right at the moment of labeling.
The image above shows our top and bottom labeler, set up with a Zebra print engine on both labeling heads, for maximum flexibility.
This system is fine to use with pre-printed labels as well – many customers buy pre-printed labels for their high volume products and use the late-stage customization technique for smaller runs.
Oh, I should mention that ID Technology is a leading manufacturer of flexo, digital and thermal labels for a wide range of applications.
On-Demand Printing for Pharma Labels.
This final example of late-stage customization involves bringing in-house the printing of labels for pharmaceutical applications.
Our colleagues at WLS produce the acclaimed Autonomy IV on-demand label printing system, ideal for meeting the demanding needs of the pharmaceutical industry.
The Autonomy system allows customers looking to implement lean manufacturing, an all-digital workflow to completely control their labeling process. Of course, it contains the levels of inspection and control that the industry demands.
Check out this video where my friend Harry Anderson at WLS explains what it’s all about:
So, late-stage customization concepts can be used in many packaging applications, to enable lean manufacturing, reduce costs and increase efficiency.
I hope you found these examples interesting – I know there are more situations where these ideas can also be put to use.
If you’d like to learn more about anything involving labeling or printing for packaging, please contact us at IDT@ProMachBuilt.com – we’ll get you in touch with the right person to help you!