Do you need to apply labels to packages such as clamshells, sealed plastic trays, or similar items?
If you do, you probably must apply labels to the package’s top or bottom, maybe both.
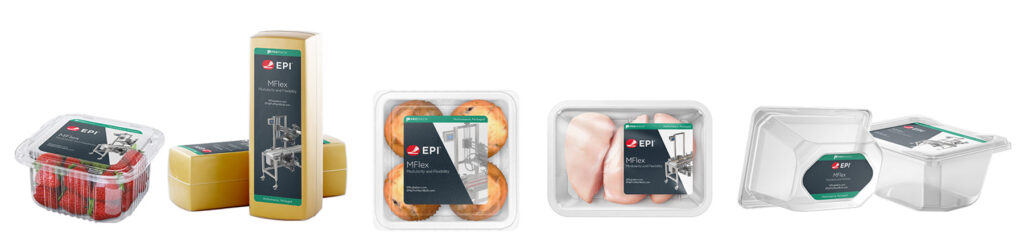
The EPI MFlex™ labeling system was designed to handle many of these applications and is ideal for labeling clamshells trays and much more. MFlex is engineered to be simple to use while also sophisticated enough for demanding conditions.
Yes, labeled from top to bottom, we’ve got you covered!
For these types of packages, three MFlex configurations are most often used.
MFlex Top & Bottom Labeler
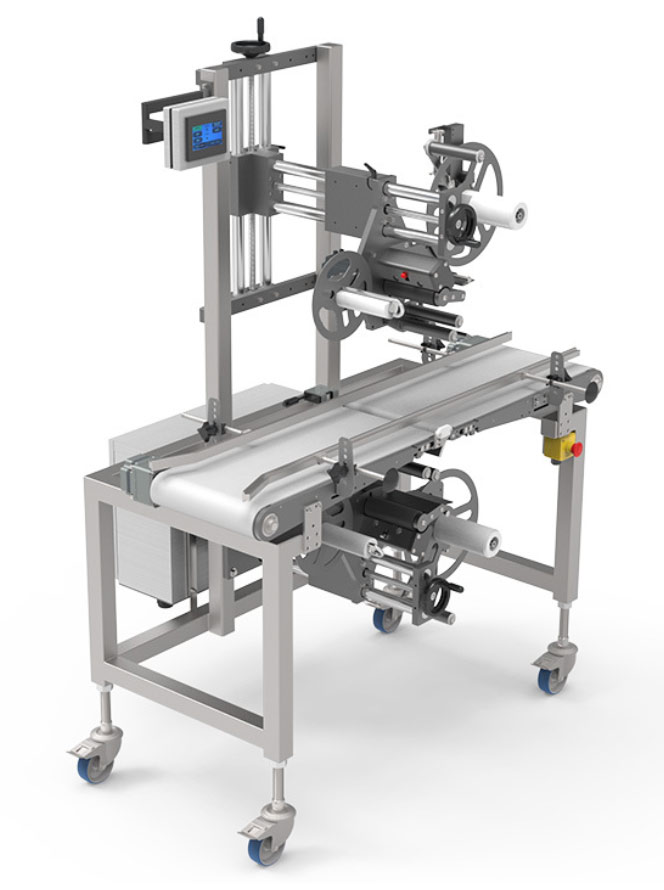
The MFlex Top & Bottom labeler utilizes two conveyor sections, with a small space between them. As the package moves over this space, the bottom label is applied, and the top label is added once the package has transferred to the second conveyor.
MFlex Hugger Belt Labeler
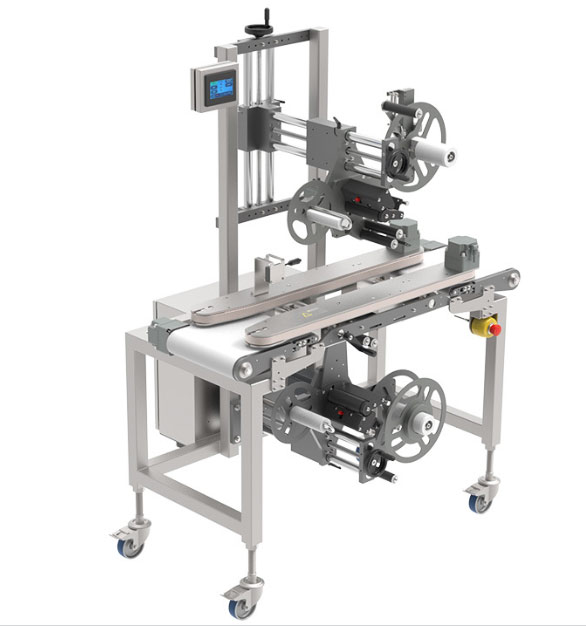
The hugger belt configuration was designed for applications where the package isn’t ideal for running on the usual top & bottom machine.
MFlex Hugger Belt is a labeling system that uses hugger belts to move the product to be labeled through the label application section of the machine. This allows for many packages to be labeled, especially when other conveyor designs make it difficult to apply the label in the required location on the package.
The hugger belt machine is highly versatile and can be configured for top labeling, bottom labeling, and both top and bottom labeling. It can also apply c-wrap labels.
This hugger belt concept can be ideal for labeling products that are light (or low-friction) and difficult to control on conventional conveyors. The design also allows barcode scanners or CIJ inkjet printers to be mounted in the open space below the belts.
If the product is very flexible, it might be challenging to grip with the hugger belts, and a conventional conveyor machine might be a better choice.
MFlex Top, Bottom, C-Wrap Labeler
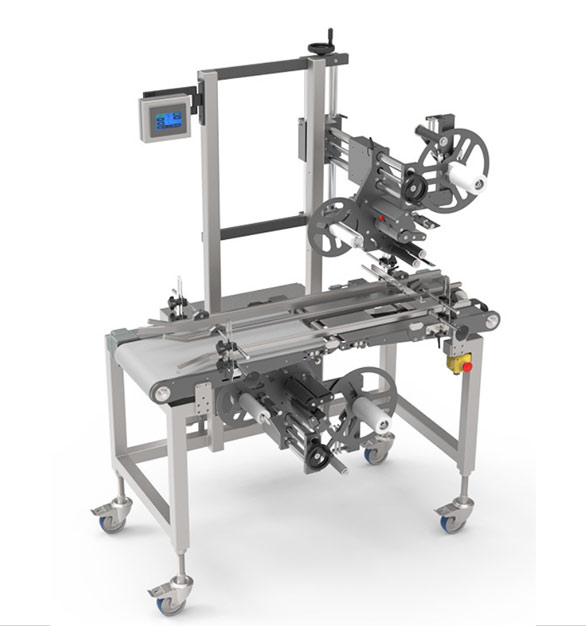
For customers that need to run more than one label configuration through the packaging line, our top, bottom, and c-wrap variant could be a good option.
This MFlex labeler can be easily switched from top/bottom labeling to applying c-wrap labels in just a few minutes – ideal for co-packers and others needing more flexibility.
Note that the hugger belt machine has this capability as well.
Optional Items
Several options can be added to these MFlex systems to match them exactly to a particular customer’s needs:
- Printer for adding date and production codes. These are usually thermal inkjet, thermal transfer overprinter (TTO) or CIJ inkjet.
- Print and apply labeling capability
- Zero-downtime options to maximize efficiency.
One Control to Rule Them All
Have you noticed that some labeling systems have multiple control interfaces, some quite complicated?
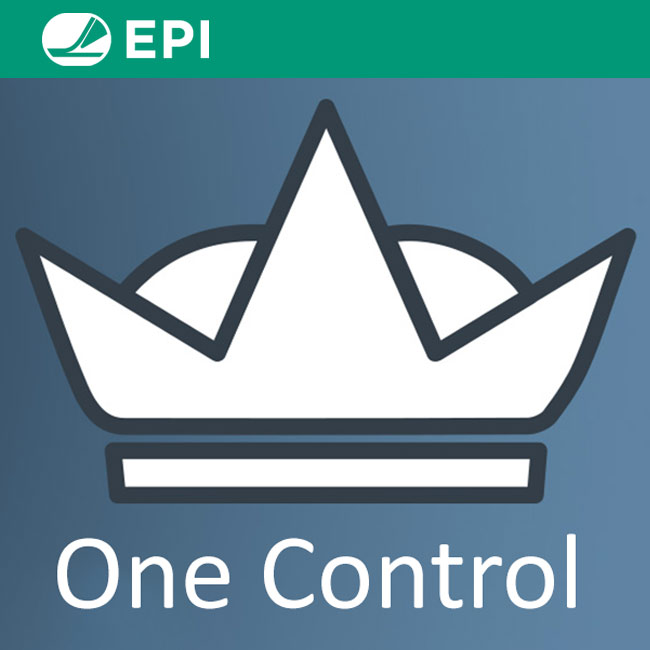
We want the operators to love the MFlex, so each labeler has a singular HMI from which the entire machine is controlled—without having to move to a different part of the system to adjust or change settings.
The system is designed to be simple for routine tasks but can also help maintenance with in-depth diagnostics when needed.
Want to reduce set-up time? It’s easy; once you have a labeling job set up and ready to run, save it as a recipe, ready to recall instantly for next time.
Syncing Outside the Box
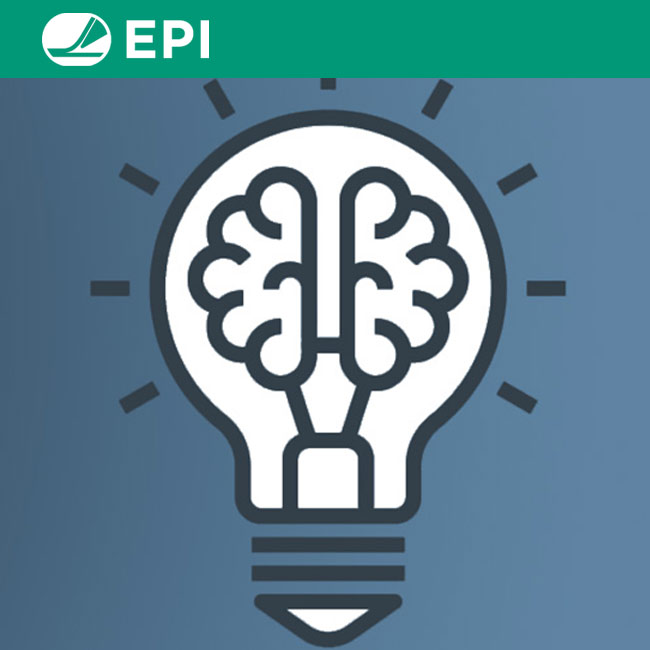
Synchronizing all the machine modules on a labeling machine is critical to getting the best results. That’s why we’ve made MFlex amazingly intelligent with its closed-loop servo drive system.
The speeds of the labeler modules are monitored constantly, and the system responds to any changes in real-time.
If the conveyor speed changes while the machine applies a label – or even stops completely – the label is still correctly positioned on the product every time.
This sophisticated system works happily behind the scenes, ensuring everything is in perfect sync while the operators can get on with other tasks.
Harsh Environment? Bring it on!
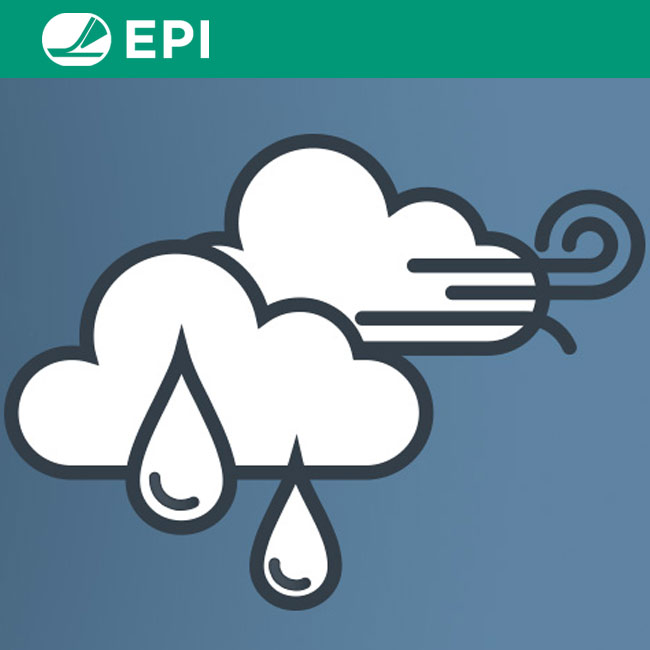
A lot of packaging equipment doesn’t have the luxury of operating in perfect conditions – sometimes the areas where machines such as labelers are installed are wet or dusty – maybe the equipment has to be washed down for sanitation.
That’s why we engineered our MFlex machines to meet IP65 protection standards right out of the box. No need to pay extra or to specify optional features. Every MFlex is built on the understanding that it might have to work in less-than-perfect conditions.
Even if your packaging line is set up in a friendly environment, having your labeler designed to this standard will help prolong its service life.
Meet the Mod Squad
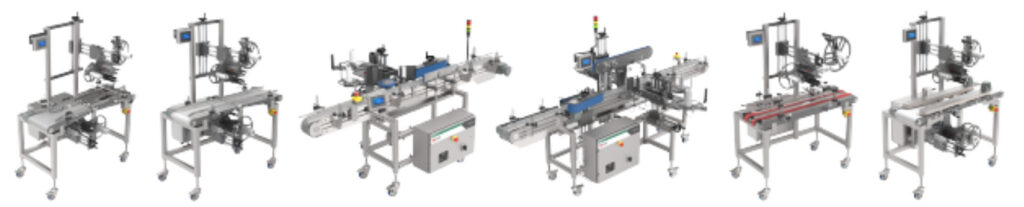
The MFlex labeling systems are members of our Mod Squad – a range of flexible and modular labeling systems designed to handle the most common labeling applications.
All MFlex models share many of the same features:
All MFlex models share many of the same features:
- The same well-engineered anti-corrosive frame and construction.
- All have the same singular HMI and screens, optimized for ease of use.
- The standard IP65 environmental protection is right out of the box.
- Common motors and motion control modules through the range.
- Being part of ProMach Labeling & Coding, EPI has extensive sales and technical support across North America.
MFlex labeling systems are built here in the USA, in our manufacturing plants in New Freedom, PA, and Oakland, NJ.
If you want to learn more about the MFlex configurations, just contact us at EPI@ProMachBuilt.com; we’d love to help!