To start, what is a print engine?
To use an automobile analogy, the print engine is really the “engine” of a Panther Industries print and apply labeling automation system. The print engine not only prints the information onto the label (e.g., shipping information, barcode, etc.), it pulls the label stock from the let-off assembly and peels the label from the liner material so it can be presented correctly to the label applicator. Panther Industries utilizes two different brands of print engines in our systems – SATO, and Zebra. Our systems are designed so that either of those brands of print engines will work within it, and are easily swapped/replaced when necessary (e.g., due to age, damage, or maintenance).
In short, a print engine drives the label print and feed process.
Print engines are manufactured in a couple of different sizes – typically they are either 4″ or 6″ in width. The size of print engine required in a labeling system is directly dependent on the width of the label that is being applied to the item.
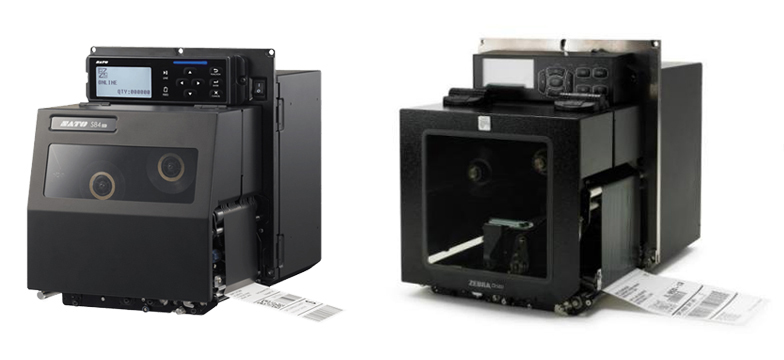
What are the most common issues a customer or end user will see with their print engine?
The three most common issues we hear in service calls and emails are related to the following:
Calibration Issues – Multiple/Blank Labels Fed from Print Engine
A customer or end user having calibration issues usually sees a blank label unexpectedly follow a printed label. This is typically related to the gap sensor in the print engine not “seeing” the gap between labels. This gap recognition is important because it tells the print engine where one label ends and another one begins. Recalibrating the print engine assists it in recognizing that gap between labels.
Label Presentation – Label Too Far Behind or Too Far Forward in Relation to the Peel Bar
We will hear customers tell us “labels are not coming out onto the applicator all the way (or too far)” after printing has occurred. This can be a result of a label presented too far behind or too far forward of the peel bar, resulting in the label not staging correctly on the label applicator. This can cause the label to apply incorrectly to an item, or in an incorrect location. This issue can be caused by worn rollers within the print engine. To continue the automobile analogy, think of what happens when your tires are worn and become bald. They have less traction and can slip or slide on the road surface. The same is true for these rollers. As the rollers become worn, or if label residue builds up, the label stock is not gripped correctly when feeding through the print engine and the labels are presented short or past the peel bar.
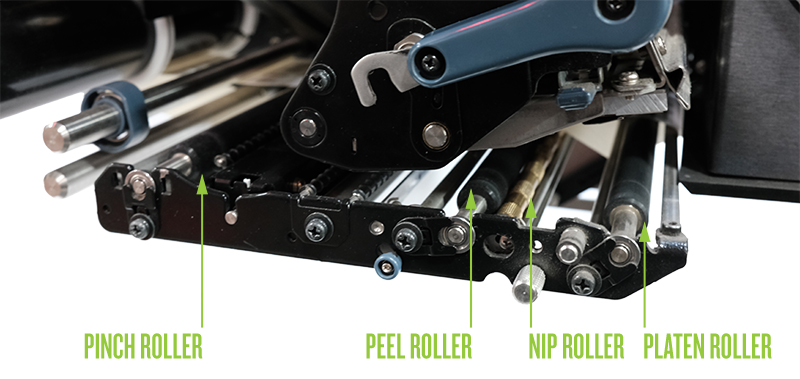
The three key rollers that help the labels feed through the print engine – shown above – are the platen roller, the pinch roller (near the gap sensor), and the peel roller. Over time, these rollers become worn from regular use and can have a negative impact on how the label is presented to the applicator after it is printed. In addition, there is a nip roller – the knurled roller on the nip assembly – where labels can build up, leading to stalling or slippage of the peel roller. Regular inspection and cleaning of the nip roller is recommended every time you change labels on your system.
Another issue related to the labels not presenting to the peel bar correctly may have to do with the wear of the belts within the print engine. If the belts that drive these rollers wear down, they can also affect the rollers presenting the label to the peel bar correctly. Belt replacement is typically performed as needed, but higher volume customers (printing 5,000 labels per system per day) should consider replacement of their belts on an annual basis.
All of these rollers and belts should be regularly inspected and cleaned to ensure they are in optimum working condition. In addition, we recommend cleaning these rollers and belts with 99% isopropyl alcohol every time a roll of labels is replaced. Also, be mindful not to use sharp objects to clean these components, as they can damage the rollers and cause unintended slippage or poor print quality. Best practices also indicate these rollers should be replaced after every 2 printhead changes. Regular preventative maintenance and cleaning steps can help extend the life of your print engine’s rollers up to 3 or 4 times longer and avoid costly downtime.
Print Quality – Poor Quality of Information on Label
If you are experiencing blank sections or areas of missing information on your labels, your printhead may be due for replacement. Over the course of a printhead’s life, its elements will eventually wear out and stop producing an image in areas (see example below).
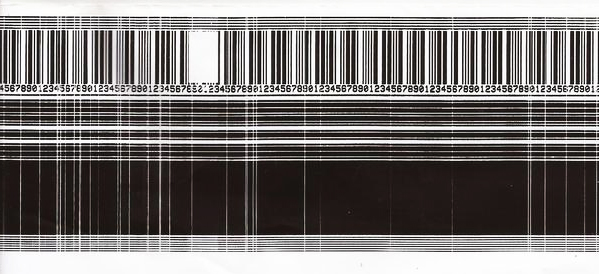
The lifespan of a typical print engine printhead will account for imprinting approximately 1,000,000 to 1,500,000 linear inches of label material. The rate at which you need to replace your own printhead will obviously depend on the number of items that are labeled in your operations. Labeling systems applying to cartons within an e-commerce facility are probably going to see faster wear on their printhead than a company that applies labels to pallets.
For example, if your operation prints 10,000 6″ long shipping labels daily, then you are running 60,000 linear inches of labels per day. Given the printhead’s life expectancy, your printhead may only last 16 to 25 days. If you are printing and applying these same 6” long labels to pallets at 300 items per day – equating to 1,800 linear inches per day – your printhead may last 1.5 to 2 years.
Printhead life can also depend on cleaning schedules, quality of materials used, and overall operational environment, so the examples above may not be applicable for every instance. For good preventative maintenance practices, we recommend regular inspection and cleaning of your printhead. Cleaning your printhead after every ribbon change (or after every label roll change with direct thermal labels) can help extend the life of your printhead up to 3 or 4 times longer.
Given their importance in our print and apply systems, do customers or end users purchase spare print engines or parts?
Yes. We highly recommend that a spare print engine is purchased to have on hand in the event the primary unit(s) has any issues that cannot be resolved with routine maintenance or service. This is especially important in facilities that utilize multiple print and apply labeling systems. Much like you carry a spare tire in your car in the event of a flat, having a spare print engine as a backup allows you to minimize downtime. If a print engine is ever damaged and cannot be repaired/serviced while still within the labeling system, they are easily swapped for a new/replacement unit.
Panther Industries also offers depot repair services for print engines. This means the end user ships us their print engine so our expert service technicians can repair the unit and send it back so you are up and running again, quickly.
Lastly, we also sell spare parts kits for print engines that include the key rollers, belts, and printhead mentioned above.
To order spare parts, or obtain information on print engine depot repair services, please contact our parts department at Panther.Parts@promachbuilt.com or toll-free at 800-530-6018, x175. You can also view more of their coding and labeling solutions on our website.