Using inkjet printers to add variable information to shipping cases, is increasing in popularity. Using this technique can dramatically reduce the number of pre-printed items that need to be managed and fit into company efforts to increase digitalization and move to a lean workflow.
Here at ID Technology, we have a lot of experience when it comes to installing inkjet systems for printing barcodes, text and graphics onto corrugated cases. We are a founding distributor of the FoxJet ProSeries system and have won the prestigious Regency Award for top FoxJet distributor for 14 consecutive years.
If there is one thing we’ve learned over this time, it’s that having good product handling is as important as having good printing equipment for getting the high-quality, compliant GS1 barcodes that customers demand. If the boxes are not presented consistently and accurately to the printheads, this will show in poor print quality and in particular will not allow high-quality barcodes to be printed.
To help educate users on best practices for product handling, our friends at FoxJet recently produced a detailed whitepaper on this topic that goes over many of the issues that are important to ensure great quality printing every time.
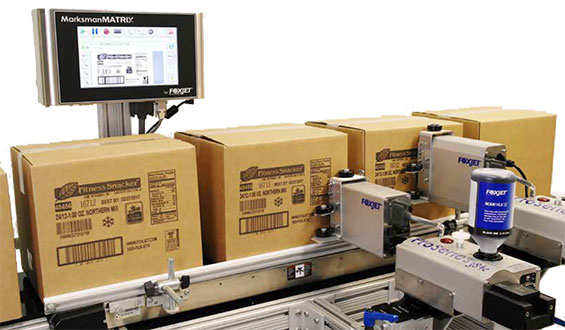
The whitepaper the transition from the case taper or sealer to the conveyor where the barcode printers are installed as being an area of crucial importance. Because space is often limited on packaging lines, the printheads often have to be installed very close to the exit of the case sealer. Some important factors are:
Carton Control – Proximity to the Printhead
It is important that after leaving the case sealer, the boxes are correctly presented the correct distance from the printheads. The drops of ink that are fired from the printheads can only travel a short distance while maintaining accuracy. If the box is too far away, print quality will decline and if so close it hits the printhead, damage might occur.
Be sure to control the boxes gently so that the boxes are undamaged as they pass through your packaging processes.
It’s best to use guide rails to accurately control the position of the box and even better use in conjunction with FoxJet’s retracting printhead brackets. This bracket uses a roller allow the printhead to be the correct distance from the box every time.
Product/Conveyor Speed
Ensure that boxes leaving your case sealer are traveling at a speed that is within the limits of your inkjet printer. Our FoxJet ProSeries printheads are able to print high-quality text, barcodes and images at up to 300ft per minute, which is enough for all but the fastest production lines.
Angel Hair
No, we are not talking pasta here! Some case sealing machines use hot melt adhesive to hold the flaps on the boxes closed. At times the adhesive applicators can leave a stringy residue behind that can get stuck to the printheads and block the tiny nozzles. Dust from the corrugated boxes can be bad too – be sure to regularly clean your packaging equipment and the printheads.
Vibrations
Good quality printing depends on the boxes being transferred smoothly past the printheads. Make sure your conveyor belt runs smoothly and that you are not dropping boxes onto the conveyor where the printheads are mounted. We’ve seen this happen and the results are not always pretty!
Best Practice of All
The best way to get the best labeling or coding for your shipping cases is to connect with your local ID Technology representative. With many years of experience, combined with the case packing, sealing and product handling of ProMach, we are able to help you determine the best solution for all your case coding or labeling needs.
How can ID Technology and ProMach help you meet your objectives for your packaging barcode and coding operations? Contact us today at 888-438-3242 Option#3. You can also email me at dholliday@idtechnology.com. We’ll be sure to get you in touch with an expert, right in your area!